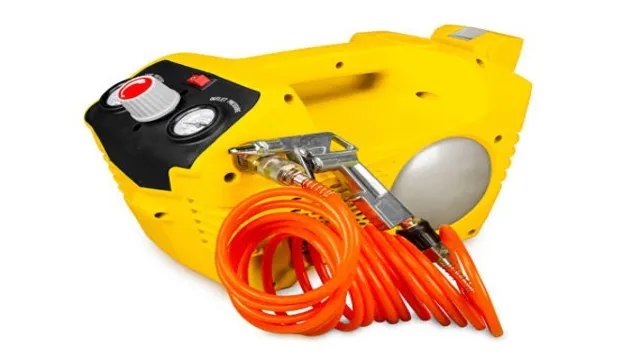
Have you ever wondered how an air compressor knows when to stop pumping air into the tank? Enter, the pressure switch – a critical component that plays a crucial role in the proper functioning of your compressor. Simply put, a pressure switch acts as a controller that turns the compressor on and off based on the pressure levels within the tank. Without it, you could be risking potential damage to your compressor or even worse, injury.
In this blog post, we’ll break down the intricate workings of pressure switches and explain how they ensure that your compressor runs smoothly and efficiently. So, hold onto your hats and let’s get started!
What is a Pressure Switch?
If you want to know how does a pressure switch work on an air compressor, then you’ve come to the right place. In a nutshell, a pressure switch is a device that’s designed to monitor and regulate the air pressure inside a compressor tank. It does this by activating or deactivating the electric circuit controlling the electric motor once a certain pressure level is reached.
Typically, a pressure switch is connected to a pressure gauge and a relief valve, which work in conjunction to maintain the pressure inside the tank within a safe and efficient range. When the pressure drops below a predetermined level, the pressure switch turns the compressor motor on, and it starts pumping air into the tank until it reaches the desired pressure level. Conversely, when the pressure exceeds the set limit, the switch shuts off the motor to prevent the tank from over-pressurization.
This is how a pressure switch on an air compressor ensures optimal performance and safety during operation.
Definition of a Pressure Switch
A pressure switch is a device that’s used to turn on or off a system or machine based on the pressure level of a fluid or gas. These switches are typically used in industrial settings where there’s a need to control and regulate pressure levels. When a pressure switch detects a change in pressure, it sends a signal to the system or machine, informing it to either turn on or off.
This allows for greater control and precision in processes such as hydraulic systems, air compressors, and water pumps. Pressure switches have become an essential component in many industries, including manufacturing, automotive, and construction. The key benefit of pressure switches is their ability to automate processes while also ensuring safety and efficiency.

Typical Applications for Pressure Switches
A pressure switch is an electronic device designed to detect changes in pressure and act accordingly. It works by sensing changes in pressure and then opening or closing an electrical contact point, depending on the pre-defined settings. These settings can be adjusted to meet specific needs, and various types of pressure switches are available to suit different applications.
Pressure switches are used in a wide range of industries, including hydraulic, HVAC, automation, and pump control. They are commonly used to protect equipment, optimize system performance, and ensure safety in various processes. For instance, pressure switches are often used to ensure that a hydraulic system is operating within its safe limits, to monitor water pressure in an HVAC system, or to control the flow of air in an automation application.
Whatever the application may be, a pressure switch is an essential device that helps ensure that systems operate efficiently, safely, and with the desired performance.
How a Pressure Switch Works
If you’re wondering how a pressure switch works on an air compressor, then you’ve come to the right place. Essentially, a pressure switch is a device that is designed to monitor the pressure in a tank or vessel, and automatically turn a pump or motor on and off as needed to maintain a certain pressure level. In the case of an air compressor, the pressure switch is typically located near the tank and is wired into the motor circuit.
When the pressure in the tank drops below a certain level, the switch will flip on, allowing the compressor to kick on and fill the tank with more air. Once the tank reaches the desired pressure level, the switch will flip off, shutting down the compressor until the pressure drops again. This process continues over and over as long as the compressor is in use.
The result is a steady supply of compressed air that can be used to power pneumatic tools and other equipment. So, in short, the pressure switch is a crucial component of any air compressor, allowing it to function efficiently and effectively.
Components of a Pressure Switch
A pressure switch is a critical component of many industrial and commercial applications. It works by detecting changes in pressure and converting those changes into electrical signals that can be used to control various processes, including pumps, motors, and heating systems. The basic components of a pressure switch include a pressure-sensing element, a set-point adjustment mechanism, and a switching mechanism.
The pressure-sensing element is typically a diaphragm or a piston that responds to changes in pressure. The set-point adjustment mechanism allows the user to set the desired pressure level at which the switch should activate or deactivate. Finally, the switching mechanism is responsible for turning the switch on or off based on the pressure levels detected by the sensing element.
Overall, the pressure switch is a simple yet highly effective device that has a wide range of applications in many industries. It is an essential component of many automated systems that require precise control over pressure levels for optimal performance.
Types of Pressure Switches
Pressure Switches Pressure switches are types of control systems that are used to monitor and regulate the pressure in machines and equipment. These devices work by reacting to changes in pressure and triggering switches that either turn on or turn off various components depending on the desired pressure level. The basic function of a pressure switch involves a mechanical diaphragm, which is designed to flex in response to changes in pressure.
This diaphragm is connected to a set of electrical contacts that are normally open when the pressure is below a certain threshold. When the pressure exceeds this threshold, the diaphragm flexes and closes the contacts, completing an electrical circuit and triggering the desired action, such as activating a warning light or shutting down a machine. There are many different types of pressure switches available on the market, each designed to suit different applications and pressure ranges.
Some common types include differential pressure switches, vacuum pressure switches, and air compressor pressure switches. By understanding how these devices work, businesses and industries can choose the right pressure switch for their specific needs, helping to ensure reliable and safe operation of their equipment.
Calibrating a Pressure Switch
A pressure switch is an essential component in many industrial applications, helping to maintain safe operating conditions and prevent damage to machinery. It’s a simple yet effective device that uses pressure as a trigger mechanism. When the pressure threshold is reached, the switch activates and sends a signal to a control system, which can trigger all sorts of actions, from shutting down a machine to alerting operators of potential issues.
To ensure that a pressure switch works accurately and reliably, it’s crucial to calibrate it regularly. This involves adjusting the pressure settings to match the desired output, using specialized equipment and techniques. By calibrating a pressure switch, you can ensure that your process is running smoothly, reduce the risk of accidents or breakdowns, and save time and money in the long run.
So, whether you’re dealing with air compressors, boilers, or hydraulic systems, it’s essential to keep your pressure switch calibrated and in good working order.
Installation and Maintenance
Are you curious about how a pressure switch works on an air compressor? Well, let me break it down for you. First off, a pressure switch is designed to monitor and regulate the pressure levels in your air compressor. It is typically installed on the side of your compressor and connected to the motor through electrical wiring.
When the pressure in the tank reaches a certain level, the switch will automatically stop the motor, preventing the compressor from over-pressurizing. Once the pressure drops to a certain level, the switch will turn the motor back on, allowing the compressor to build up pressure again. Essentially, the pressure switch acts as the brain of your air compressor, constantly monitoring and controlling the pressure levels to ensure optimal performance and prevent any damage.
It is crucial to keep your pressure switch maintained and regularly checked to avoid any potential malfunctions or failures that could lead to serious safety hazards. So, next time you hear your compressor kick on and off, remember it’s all thanks to the handy pressure switch keeping things running smoothly.
Installation Steps for a Pressure Switch
Installing a pressure switch is an essential task for every homeowner or business owner that relies on proper water supply or irrigation. The first step in installing a pressure switch is turning off the power supply to the water pump. Next, connect the pressure switch to the water line and ensure that the wires are connected correctly.
The pressure switch may require calibration, and it is always best to refer to the manual for the specific instructions. Once the pressure switch is installed correctly, turn the power supply back on and test the system. Regular maintenance is also necessary to ensure that the pressure switch is working correctly.
Clean the switch and its components regularly and check the system’s pressure and volume to avoid any issues. Overall, proper installation and maintenance of a pressure switch can save property owners from expensive damages caused by erratic water pressure or complete system failure.
Testing and Troubleshooting the Pressure Switch
When it comes to the proper functioning of your pressure switch, installation and maintenance are key. Proper installation ensures the switch is in the right location and correctly wired to the system. Maintenance involves checking the switch regularly to ensure it is operating correctly and efficiently.
To test the pressure switch, you will need a multimeter to measure voltage and continuity. First, connect the meter to the switch terminals and check the readings against the manufacturer’s specifications. If the readings are off, you may need to troubleshoot the switch for any wiring issues or damage.
You can also perform a pressure test to ensure the switch is accurately sensing the pressure in the system. Remember, regular maintenance and testing can save you money in the long run and prevent any potential system failures. So, keep the pressure switch in good working order to maintain the safety and efficiency of your system.
Conclusion
In sum, a pressure switch on an air compressor is like a vigilant bouncer at a club, keeping a watchful eye on the pressure levels and ready to cut off the supply if things get too rowdy. With its finely-tuned sensing abilities and magnetic contacts, the pressure switch is the unsung hero that ensures your compressor runs like a well-oiled machine. It’s the ultimate wingman for your compressed air needs.
“
FAQs
What is a pressure switch on an air compressor?
A pressure switch on an air compressor is an electrical device that controls the on/off function of the compressor motor based on the pressure inside the tank.
How does a pressure switch work on an air compressor?
A pressure switch works by sensing the pressure inside the tank and when it reaches a preset level, it activates the electrical contacts that turn on the compressor motor. When the pressure drops to a lower preset level, the contacts open and the motor turns off.
What are the different types of pressure switches used on air compressors?
The most common types of pressure switches used on air compressors are differential pressure switches, vacuum switches, and pressure transducers.
What is the purpose of adjusting the pressure switch on an air compressor?
Adjusting the pressure switch on an air compressor is necessary to ensure that the compressor turns on and off at the correct pressure levels. This helps to prolong the lifespan of the compressor and prevent any damage due to over-pressurization.
How do I troubleshoot a faulty pressure switch on my air compressor?
You can troubleshoot a faulty pressure switch on your air compressor by checking the electrical connections, inspecting the switch for any damage, testing the contacts with a multimeter, and replacing the switch if necessary.
Why does my air compressor not turn on even though the pressure switch is working?
The air compressor may not turn on even though the pressure switch is working due to issues with the motor, power supply, or other components in the electrical system.
How often should I replace the pressure switch on my air compressor?
The pressure switch on your air compressor should be replaced every 5-7 years or if it shows signs of damage or wear and tear.
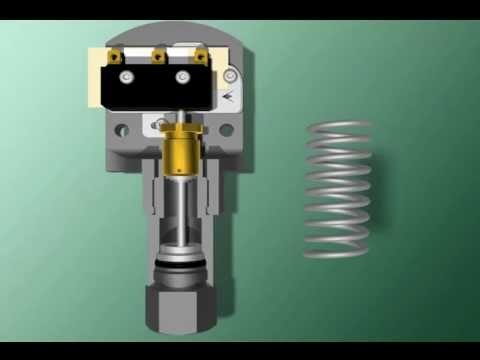